SOLUTIONS
Knowledge
Guide to Selecting an End Mill for Aluminum Machining
Guide to Selecting an End Mill for Aluminum Machining

Manufacturers make hundreds of different types of end mills for aluminum machining. And because of this, it can be hard to know which to choose for your application.
The good news is that there isn’t usually one right answer unless you are doing very specialist work. In most cases, you have a range of options that will fit the bill.
In this guide, we take a look at aluminum as a material, and then how to select a suitable end mill for drilling into it.
- Aluminum Material Profile
- Selecting Standard 1: Geometry
- Selecting Standard 2: Coatings
- Selecting Standard 3: Flutes
- Selecting Standard 4: Angle
- Speed Tiger N End Mills for Aluminum
Aluminum Material Profile
Aluminum is one of the most machined materials on the planet. Not only is the metal abundant in the Earth’s crust, but it is also extremely light and flexible, making it ideal for numerous applications across industries.Furthermore, manufacturers love the metal because it is easy to machine. Aluminum is suitable for advanced milling techniques of the kind found in most factories.
2 Types of Industrial Aluminum
There are two general types of industrial aluminum: cast and wrought. Cast aluminum offers higher flexibility and lower tensile strength. It costs less to produce and contains significant quantities of other elements, including magnesium and silicone.Wrought aluminum is a purer metal, making it less abrasive. It is highly heat-resistant and offers superior machinability compared to cast.
Follow our guide to find your right end mill for aluminum is so easy
If you are looking to machine aluminum as a one-off, making the right end mill selection doesn’t matter a great deal. Most tools will get the job done. However, if you are looking to mill thousands of items per week, then your choice of bit matters considerably. Making incorrect choices could dramatically increase production costs and affect the quality of the finished product. The main challenge in machining aluminum milling is heating. Compared to steel, aluminum has a much lower melting point. Because of this, a friction-induced fusion between the end mill and material can occur, destroying both the piece being milled and the equipment. Therefore, choosing end mill with the correct geometry, coatings, flutes, and angles, is essential.
Here’s everything you need to know about end mill standards for aluminum:
Selecting Standard 1: Geometry
End mills comprise a shank, neck, flute, and edge. The flute is the section of the bit that contains the cutting edge. It runs from the tip of the bit all the way to the shank. The shank is the part of the tool that does not have an edge. It is just a cylindrical piece of metal from which manufacturers cut the flute. The geometry of the end mill typically refers to its basic shape and design. The shape you choose will typically depend on the nature of the machining you want to do, and not the material itself.
For example:
- Square end mills, also known as flat end mills, are for plunge cutting, profiling, slotting, and side milling
- Long neck end mills reduce interference between the workpiece and the tool and are usually for pocketing
- Ball nose end mills are for when you want to create rounded contours and flat-bottomed pockets
- Corner radius end mills are usually reserved for milling molds and dies, since getting flat-bottom pockets and rounded contours don’t require as many tool changes with these
- Taper end mill for making grooves and holes, and for side-milling at an angle.
Besides general shape, various tooling options are also available for end mill. Chipbreaker tools, for instance, improve chip evacuation. Standard two- and three-flute mills (discussed below), have serrated edges designed to scoop chips from cutting surfaces and run at higher rates for better feed performance. Off-set chip breaker geometry reduces chip size for enhanced evacuation while leaving workpiece surfaces semi-finished.
High balance end mills are also available. Manufacturers create these to improve the performance of machining tools capable of higher feed rates and revolutions per minute (RPM). These feature radically altered bit shapes, allowing cutting to take place at up to 33,000 RPM.
To manage heat, many high-balance end mills have coolant-through systems to keep blade temperatures down. Manufacturers also sometimes equip them with chip breakers for high-efficiency milling applications.
Selecting Standard 2: Coatings
Coatings are end mill bit finishes designed to increase hardness, reduce abrasive wear, prolong the tool’s life, and create a thermal barrier between the bit at the workpiece. Some coatings may also improve waste material evacuation, reducing friction damage further. However, coating materials suitable for use with aluminum are minimal. Because aluminum is a soft metal, end mill coatings do not need to provide much additional hardness. You can get good results drilling aluminum raw. However, because of the metal’s low melting point, coatings are required to reduce excess heat in some situations.
TB - or tetrabond diamond coating - has a high lubrication coefficient and keeps chips moving out of the material, reducing the need for coolant. It can also increase tool life because of the natural hardness of diamond material.
Aluminum chrome-nitride + silicon nitride (nACRo) are also suitable for high-heat applications. nACRo protects bits against abrasion and has a heat resistance of up to 1100° before it begins to break down.
Generally speaking, zirconium nitride (ZrN) is used for abrasive aluminum alloys. Amorphous diamond improves lubricity and wear, and prevents edge rounding, offering superior performance in non-ferrous metal applications.
Selecting Standard 3: Flutes
When it comes to choosing end mills for aluminum machining, flutes are perhaps the most important consideration. They remove aluminum chips from workpieces, preventing them from cluttering the material. Flutes refer to the number of cutting blades that emanate from the end mill tip and spiral down its body. For instance, a single-fluted end mill would have a single cutting edge, whereas a two-flute mill would have two, and so on.
The number of flutes an end mill has determines its rigidity, chip evacuation capacity, wear time, vertical accuracy, and performance on both soft and hard materials. Generally speaking, the more flutes, the more rigid the bit is. However, chip evacuation performance goes down. One-flute end mills have poor wear time, vertical accuracy, and surface roughness compared to six-flute versions. On the other hand, they tend to have better performance when machining softer materials, such as aluminum.
Aluminum end mills usually come in two- or three-flute varieties. Lower flute counts result in excessive wear while higher counts would prevent chip extraction during high-speed drilling. However, as you will discover below, there are some exceptions.
Whether you choose two- or three-flute end mill depends on the type of work you want to do. Two-flute end mills have long been the standard for aluminum milling, while three-flute varieties are better for finishing.
Ultimately, the decision boils down to preference and experience. Higher rigidity can improve wear and tear, while lower flute counts improve chip removal rates
Selecting Standard 4: Angle
The helix angle is the angle between the mill’s centerline and the tangent of its cutting edge. End mills with shallower angles have cutting edges that coil around them more slowly than those with higher angles. Helix angles matter a great deal for aluminum machining. For aluminum cutting, machinists typically use 45°, 50°, and 55° helix angles. These tend to generate the least chatter and offer the best balance between rigidity and chip extraction. Some professionals may choose to use variable helix angle bits for more reliable operation when drilling at depth.
Shallow helix angles of 15° offer excellent chip removal and cutting torque, but they remain weak in terms of axial tension. Steep helix angles of more than 55° offer exceptional axial tension, but cutting torque is often too low for many aluminum machining applications.
For finishing, machinists will typically choose 45° bits as the shallower cutting edges attack the material more aggressively. Chip removal is okay, but axial tension is higher.
Speed Tiger N End Mills for Aluminum
Speed Tiger has developed a wide array of end mills for aluminum.
AP Square End Mill

For instance, the AP Square End Mill is a purpose-built aluminum cutting tool made by an ISO-9001 factory designed with a single flute for higher chip extraction. The exterior of the end mill is reinforced to add extra strength and durability in high-intensity applications.
★ Single Flute AP is designed for
① High-speed machining and high-volume material removal
② Excel at working Wood, Aluminum, Copper, Plastic, Brass, carbon steels (~HB225), alloy steels (HB225~325), and pre-hardened steels (up to HRC45).
③ The geometry and large chip groove effectively remove chips allowing for higher feed rates and shorter cycle times.
AL Carbide Drill for Aluminum Applications

Speed Tiger also offers “N” products for non-ferrous applications (such as aluminum). The AL Carbide Drill for Aluminum Applications features a double-margin flute with a cutting edge on both the first and second blades. The design’s high rigidity improves smooth surface drilling and high-precision straight cutting while boosting chip removal. Speed Tiger also enhances accuracy by reducing the space between the drill tip and the start of the cutting blade.
★ Special design of AL drill
①Double margin- the second margin also has a cutting edge - Achieves smooth surface of drilling and allows high precision straight cutting.
②High rigidity design and the room for chip removals greatly improved.
③Improved the margin-top position, to advance the drilling precision.
ALC Carbide Drill for Aluminum Application

Speed Tiger's ALC Carbide Drill for Aluminum Application has the same double-margin cutting edge for high-precision straight cutting and smooth surface drilling as the AL. However, it also features a helpful coolant hole to keep temperatures down during high RPM applications. The improved margin-top position improves hole accuracy for both aluminum and copper alloy workpieces.
N-series drill bits are suitable for a wide range of aluminum and aluminum alloys, including A7075, AlZnCu1.5, AC, ADC, and A1070.
★ Special design of ALC internal coolant drill
①Double margin- the second margin also has a cutting edge - Achieves smooth surface of drilling and allows high precision straight cutting.
②High rigidity design and the room for chip removals greatly improved.
③Improved the margin-top position, to advance the drilling precision.
AUE High Feed U-Type for Aluminum Application

AUE High Feed U-Type, a sharp aluminum alloy tooth design applicable for roughing and finishing. With the special U-Type design, the material removal rate (MRR) and surface finishes are greatly improved due to effective chip removal at high rate. Strong tooth with double relief angles ensure an excellent production rates become 100% due to the improvement of tooth hardness.
★ AUE carbide end mill is designed for
① Cut faster thanks to superior Material Removal Rate (MRR) especially when slotting.
② High-feed U-type design makes these cutters ideal for working with aluminum and copper alloy.
③ STRONG TOOTH WITH DOUBLE RELIEF ANGLES - Attain excellent production rates thanks to improved tooth hardness.
④ TOOTH DESIGN OPTIMIZED FOR ALLOYS - Surface finishes are greatly improved no matter if you are roughing or finishing due to effective chip removal.
Model | Type | Function | Helix Angle | Size Range | Coolant Hole | Coating Option |
AP | End Mill | Milling | 30° | mm: 1~12 inch: 1/4"1 |
N/A | Uncoated ZrN TB (=DLC) |
AL | Drill bit | Drilling | 20° | 5XD: 3~12mm | N/A | Uncoated TB (=DLC) |
ALC | Drill bit | Drilling | 15~20° | 5XD: 3~12mm 8XD: 3~12mm |
Yes | Uncoated TB (=DLC) |
AUE | End Mill | Milling | 50° | mm: 1-12 inch: 1/8''~5/8'' |
N/A | Uncoated ZrN TB (=DLC) |
■ More Information & Tips about CNC End Mill:
Related Article: The Beginners Guide of CNC End Mill
If you are new to CNC processing, you may think that there are so many end mills in the catalog, what’s the difference? And which end mill should I use on my CNC machine? In this article, you will learn the basic knowledge of CNC end mills about End Mill Shapes, End Mill Flutes, Details of the end mill, and End Mill Coatings.
Related Article: Master Guide of CNC Milling: Process & Application
If you are new to CNC milling, you have probably heard of this term but be unsure what it means. In this article, you will find all the information you will need to understand what CNC milling is, how it works, its applications, advantages, and more. Read on to discover everything you need to know about CNC milling.
Related Article: Master Guide of Roughing & Finishing Cut in Machining (Differences & Usage)
Machining or cutting consists of a number of stages, taking a raw piece of material from its initial state to the desired object that it is intended to be. Multiple techniques are used to obtain the final result to ensure it is the right shape and size and has the right finishing. The processes used consist of categories such as conventional machining, abrasive cutting, micro-precision machining, and non-traditional machining. Two of the initial stages in machining are the rough cut and finishing cut, which shape the material and improve the finish of the surface. Both of these are important processes but it's important to understand the differences between them and when each one should be used.
Related Article: End Mill Cutting & End Milling - Technical Guide
End mills are a key tool for cutting, with a range of different applications. As one of the most common types of cutting tools, end mills are also unique and specifically used for the end milling process. End mill cutting and end milling are crucial in manufacturing, and being familiar with these processes and tools is a must.
About Speed Tiger |
Speed Tiger is a professional manufacturer of Carbide Cutting Tools and offers OEM Services, having rich experience in producing carbide cutting tools and processing consultants for more than 24 years.
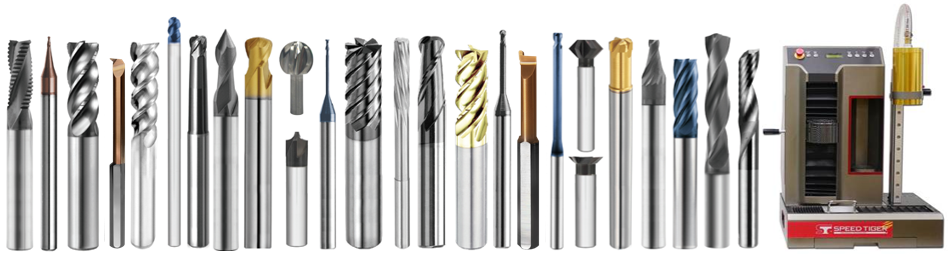
Established in 1998, Speed Tiger specialized in the production of precision carbide end mills, drills, turning tools, thread mills, and other tungsten carbide steel customized cutting tools. Speed Tiger crafts cutting tools at extreme nanometer precision +-2㎛ to the exact, enabling to achieve professional cutting quality.
Visit our shop to find out more, or check out our solution to continue learning.
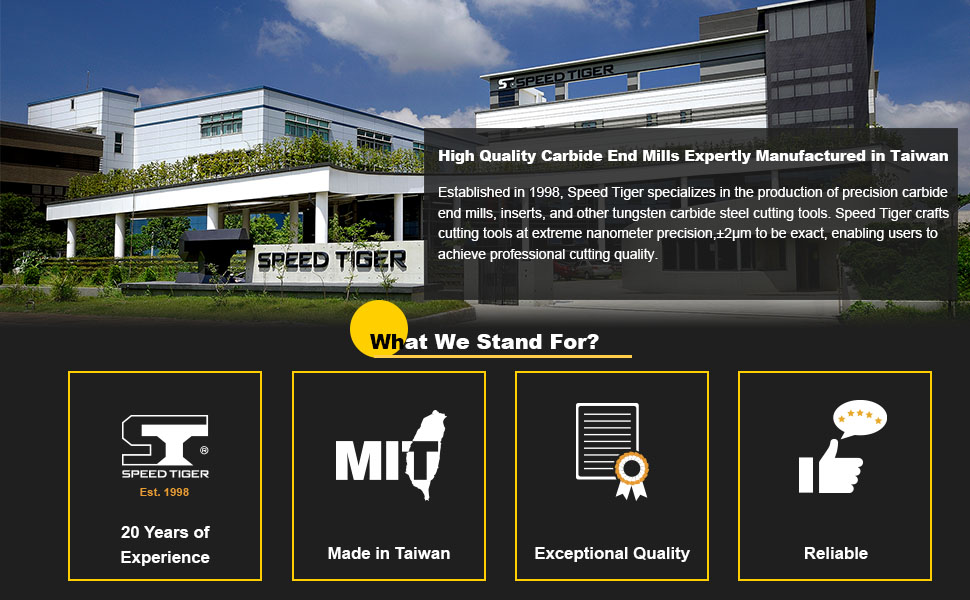
OTHER SOLUTIONS
-
Master Guide of CNC Milling: Process & Application Posted 2023-06-07