SOLUTIONS
Knowledge
Master Guide of CNC Milling: Process & Application
What is CNC Milling: Definition, Process, Machines & Operations
If you are new to CNC milling, you have probably heard of this term but be unsure what it means. In this article, you will find all the information you will need to understand what CNC milling is, how it works, its applications, advantages, and more. Read on to discover everything you need to know about CNC milling.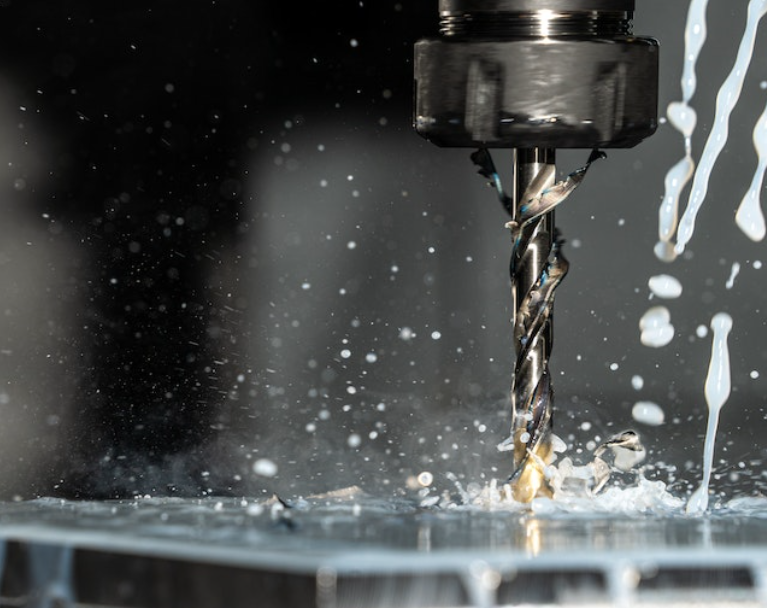
You will learn useful knowledge of CNC Milling:
- What is CNC Milling?
- What are the Advantages of CNC Milling?
- How Does CNC Milling Work? A Step-By-Step Process
- CNC Milling Machines & Parts
- Machines Axes in CNC Milling
- Most 5 Common Types of CNC Milling Operation
- Other types of CNC Milling Operations
- What Material is Best for CNC Milling?
- Applications of CNC Milling
- How to Choose the Right CNC Milling Cutting Tools & Services
What is CNC Milling?
Before we go any further, it is helpful to explain precisely what CNC milling is.CNC stands for computerized numerical control. So, CNC milling is computerized numerical control milling. CNC milling refers to a type of CNC machining process and is one of the most widely used forms of this technology.
In the CNC milling process, the cutting tool moves across a stationary workpiece following a pre-programmed design. CNC milling is described as a subtractive form of machining technology; this is because it removes material to create the design.
A CNC mill consists of computer numerical controlling systems (CNC) working in combination with a milling cutter. The combination of these elements delivers precision cutting capabilities that are essential in applications across many industries.
What are the Advantages of CNC Milling?
Using the CNC milling process offers a host of advantages; here are the main benefits:- Works independently - After the machine has been pre-programmed, it can work independently to produce parts without continuous supervision.
- Reduced labor costs - Specialized operators are needed to program the CNC mill but do not need to constantly oversee the production process.
- Increased precision - As the CNC mill follows an exact design, the component parts it produces are incredibly precise.
- Consistent results - Due to the CNC mill using a pre-programmed precise design, it delivers consistent results every time without human error.
How Does CNC Milling Work? A Step-By-Step Process
You may be wondering how CNC milling creates finished products. CNC milling follows a very similar process to many other types of CNC machining. Here are the four main steps the CNC milling process follows:1. Design a CAD Model
The first step taken is the creation of a CAD (computer-aided design) model for the component part that needs to be manufactured. The design model can be either 2D or 3D and is created using a design program.2. Generate Instructions
Once the CAD model is complete, this design is transformed into a set of instructions the CNC machine can interpret to reproduce the model. The instructions are generated using CAM (computer-aided manufacturing) software. These instructions will detail every stage of the production process and the order in which things need to happen. This will include specifying which CNC milling tool should be used when to use coolant, and what speed to use.Once the 3D model has been processed using CAM software and the instructions have been created, you will have a CNC program ready for the operator to load onto the CNC machine.
3. Complete the CNC Milling Machine Set Up
Before running the CNC program, it is time to complete the set-up of the CNC milling machine. The workpiece (material) will be loaded onto the work table, and the correct milling tool will be attached to the CNC machine.4. Start Milling
Once the CNC mill is set up, it is time to start the milling process. The operator will check that the set-up is correctly complete and will then start the CNC program so that the production of the parts can begin.CNC Milling Machines & Parts
Now we know the design model is used as the basis to create the instructions, and CAM software is used to translate these instructions ready for the machine to use, you may be wondering how the CNC milling machine itself works. To help you better understand the process, here are the main parts and components of a CNC milling machine:Frame/Base
As its name suggests, the frame/base acts as the base or foundation of the CNC milling machine. The base provides the mill with its stability.Spindle
The spindle rotates quickly and is designed to hold the machine tool. The spindle is driven by a motor.Table
The workpiece is a flat surface that sits on top of the base. The table holds the workpiece while milling takes place.Machines Axes in CNC Milling
CNC milling machines typically have between three and five axes, with five axes CNC milling machines being the most advanced. The W-axis refers to diagonal movement across a vertical plane. The X-axis and Y-axis provide horizontal movements on a flat plane, while the Z-axis offers vertical movement.3-axes milling machines
3-axes milling machines are the most commonly encountered type of milling equipment. They possess the capability to operate in the x, y, and z axes, enabling them to perform vertical cuts and machining in any direction. Nevertheless, it's essential to note that when dealing with objects like spheres, a 3-axes machine may require dividing the task into two halves due to the inability to cut from beneath the workpiece.4-axes milling machines
4-axes milling machines represent a higher level of complexity by introducing an additional dimension of movement. In addition to the standard x, y, and z axes, these machines can also rotate along the x-axis, akin to the functionality of a lathe. This rotational capability enhances their versatility for various milling tasks, making them a suitable choice for intricate operations and cut-outs.5-axes milling machines
5-axes milling machines offer the utmost versatility and sophistication in the realm of milling equipment. They excel by encompassing movement in both the x and y axes, along with rotation along two of these axes (typically the x-axis, y-axis, or z-axis). These machines are indispensable for tackling highly intricate designs and projects, such as medical device fabrication, aerospace component manufacturing, and the production of impellers. They represent the pinnacle of multi-axis CNC machinery, capable of shaping a wide range of materials and objects, limited only by one's imaginationMost 5 Common Types of CNC Milling Operation
CNC milling is always in demand thanks to its versatility and high levels of accuracy. To meet demand, there are several types of CNC milling operations that can be employed to achieve the most accurate finish:Face Milling
Face milling cutters are used to create high-quality finishes and are set in a perpendicular position.Plain Milling
In plain milling, plain milling cutters are in a position parallel to the base of the milling machine. Either narrow or wide cutters can be used, and which one is selected will depend on the size of the surface area.Angular Milling
In angular milling, single-angle milling cutters are used, and the angle is set according to the design of the part that needs to be produced.Form Milling
Form milling uses either fly cutters or formed milling cutters to produce more complex, contoured surfaces.Gang Milling
In gang milling, two or more cutters are used at the same time. The process of gang milling enables multiple cutting operations to be performed simultaneously. With more than one cutter in use at a time, production times are sped up, and complex parts are created more quickly.Other types of CNC Milling Operations
Besides the aforementioned operations, there are some Examples of the other types of milling machine operations available include:Contour Milling
When a curved or contoured surface is required, contour milling is used. Contour milling involves the rough shape of the part being produced first and a change of tools being used to create the finished contoured or curved shape.Slicing and Trochoidal Milling
The slicing and trochoidal milling technique uses the cutting tool at a perpendicular position to the surface of the workpiece. The cutting tool rotates as it moves along a circular path.Groove Milling
In groove milling, side and face milling cutters are used to create grooves in large volumes on horizontal milling machines. For vertical machines, end mills and long-edge cutters are often used.Chamfer Milling
Also referred to as beveling, chamfer milling is the process used to cut away small amounts of material from the edge of a workpiece, with the cutting tool positioned at an angle.Related Products: SPEED TIGER Chamfer End Mills & Milling Cutters
Shoulder Milling
Shoulder milling uses an end mill with multiple cutting edges with a square end to cut a flat surface. The cutting tool is set perpendicular to the workpiece’s surface.What Material is Best for CNC Milling?
CNC milling is used on many materials; some of the most commonly used materials include:- Wood
- Metal
- Glass
- Plastic
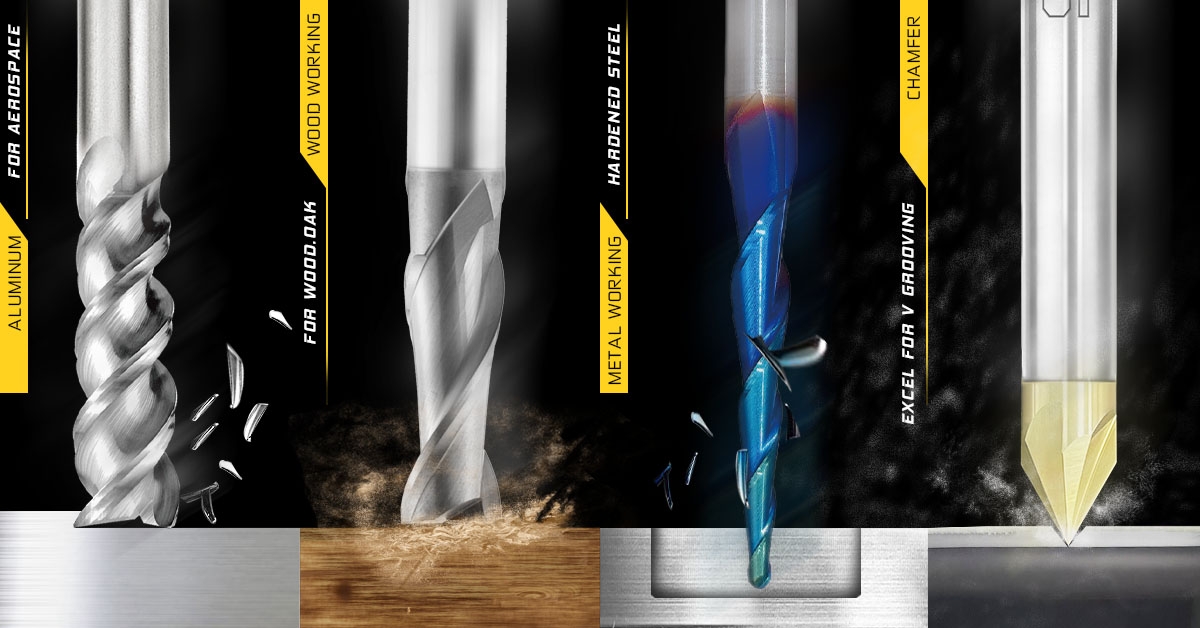
The best materials to use for CNC milling are those that offer properties best suited to the milling process, such as machinability, workability, and versatility. Materials such as aluminum and mild steel are easy to work with and offer strength without too much weight.
Applications of CNC Milling
As it can be used for a wide range of materials, CNC milling is used across many industries, these include:Product Manufacturing
CNC milling is used to manufacture components for many common items. This includes household items, such as components for televisions and smartphones, as well as the computer mainframes used by large organizations.Creation of design prototypes
As well as being used in the production of component parts in product manufacturing, CNC milling is also used during the product development stage. CNC milling can be used to create prototypes and product models, which are tested and refined throughout the development process.Aerospace
The aerospace industry utilizes CNC milling to create an extensive range of parts for aircraft. These parts include everything from fuselage structures to fuel bodies and landing gear component parts.Automotive
CNC milling is used to manufacture auto parts, such as gears, axles, piston rods, cylinders, pumps, and more.Medical
In the medical industry, CNC milling helps to meet the constant demand for new innovations. CNC milling is used to create medical instruments and tools, as well as orthotics and prosthetics.How to Choose the Right CNC Milling Cutting Tools & Services
Choosing the right cutting tools is essential to ensure you get high-quality results in every application. When it comes to using a CNC milling machine, you need to be sure you select the perfect tool for the job, and there are many different options to consider.Here are the factors to keep in mind when choosing cutting tools:
- What material is the workpiece that needs to be milled?
- What surface finish do you need?
- What size is the workpiece?
- How fast do you need the milling process to be?
The right choice of cutting tools will always be the one that takes into account the above points and is made to meet the specific needs of your application.
If you are looking for the best cutting tools, we can help. Here at Speed Tiger, we are proud to offer innovative processing solutions for our customers and can help with a wide variety of custom requests.
Whatever your processing requirements, and no matter what special machining tools you need, we can help. Whether you need CNC thread mill cutters or Solid Carbide End Mills & Mill Cutters, you can depend on us.
Contact us today to find out how we can help you and provide you with the best cutting tools designed to meet your needs.
■ More Information & Tips about CNC End Mill:
Related Article: The Beginners Guide of CNC End Mill
If you are new to CNC processing, you may think that there are so many end mills in the catalog, what’s the difference? And which end mill should I use on my CNC machine? In this article, you will learn the basic knowledge of CNC end mills about End Mill Shapes, End Mill Flutes, Details of the end mill, and End Mill Coatings.
Related Article: End Mill Cutting & End Milling - Technical Guide
End mills are a key tool for cutting, with a range of different applications. As one of the most common types of cutting tools, end mills are also unique and specifically used for the end milling process. End mill cutting and end milling are crucial in manufacturing, and being familiar with these processes and tools is a must.
Related Article: Master Guide of Roughing & Finishing Cut in Machining (Differences & Usage)
If you are new to CNC milling, you have probably heard of this term but be unsure what it means. In this article, you will find all the information you will need to understand what CNC milling is, how it works, its applications, advantages, and more. Read on to discover everything you need to know about CNC milling.
About Speed Tiger |
Speed Tiger is a professional manufacturer of Carbide Cutting Tools and offers OEM Services, having rich experience in producing carbide cutting tools and processing consultants for more than 24 years.
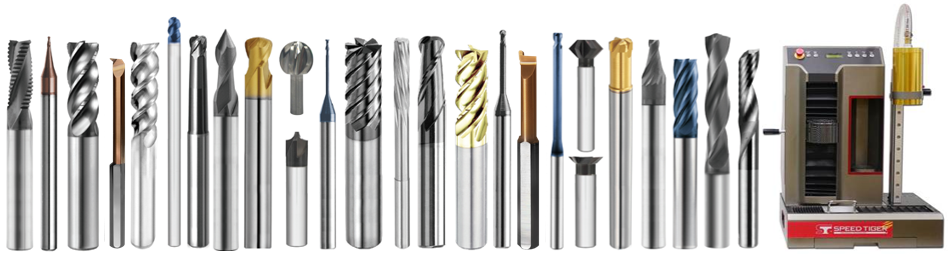
Established in 1998, Speed Tiger specialized in the production of precision carbide end mills, drills, turning tools, thread mills, and other tungsten carbide steel customized cutting tools. Speed Tiger crafts cutting tools at extreme nanometer precision +-2㎛ to the exact, enabling to achieve professional cutting quality.
Visit our shop to find out more, or check out our solution to continue learning.
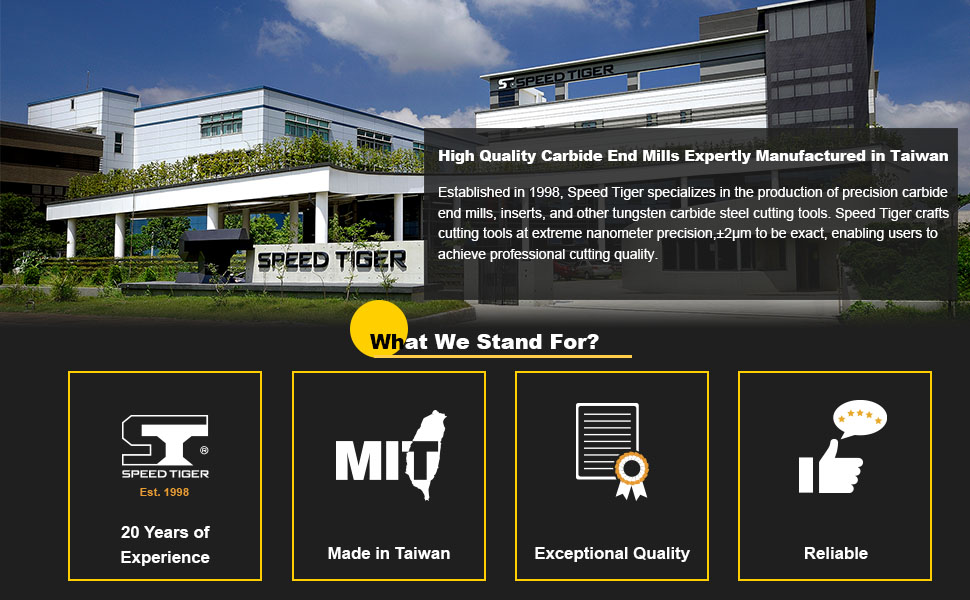
OTHER SOLUTIONS
-
Guide to Selecting an End Mill for Aluminum Machining Posted 2022-06-30