SOLUTIONS
Application
Mastering Chip Control: Unlocking the Potential of End Mills with Chip Breakers
Mastering Chip Control: Unlocking the Potential of End Mills with Chip Breakers
In this article, you will learn what a chip breaker is and provide information on its purpose, advantages, disadvantages, and usage scenarios.
A chip breaker, also known as a chip breaker groove or chip flute, is a design feature found on cutting tools, especially milling cutters. Its primary function is to control and break the chips that are produced during the machining process. The chips refer to the material that is removed from the workpiece by the cutting tool.
Purpose of a Chip Breaker:
Chip Control: One of the main purposes of a chip breaker is to control the formation and flow of chips during machining. By introducing grooves or flutes on the cutting edge, it helps to regulate the size, shape, and direction of the chips, preventing them from becoming long, unmanageable, or tangled. This improves the overall machining process and helps prevent issues such as chip jamming, tool damage, or poor surface finish.Advantages of Chip Breakers:
1. Improved Cutting Efficiency
Chip breakers facilitate the effective evacuation of chips from the cutting zone, preventing chip recutting. This improves cutting efficiency, reduces cutting forces, and minimizes heat generation, which can extend tool life and enhance machining productivity.2. Enhanced Surface Finish:
By breaking chips into smaller, more manageable pieces, chip breakers help prevent the formation of long, continuous chips that can cause scratches or marks on the workpiece's surface. This leads to a better surface finish and improved product quality.3. Increased Tool Life:
Proper chip control through chip breakers can help reduce tool wear and damage. By preventing the chips from rubbing against the cutting tool, chip breakers minimize friction and heat generation, resulting in longer tool life and reduced tool replacement costs.4. Improved Chip Evacuation:
Chip breakers promote better chip evacuation from the cutting zone, which reduces the risk of chip accumulation and clogging, especially in deep or narrow slots. This enables uninterrupted machining and reduces the need for frequent tool stoppages to clear chips.Disadvantages of Chip Breakers:
1. Design Complexity:Incorporating chip breakers into cutting tools adds design complexity and manufacturing costs. The precise design and positioning of the chip breaker feature require careful consideration to ensure optimal chip control and performance. This can increase the overall cost of the cutting tool.
2. Limited Applicability:
Chip breakers may not be suitable for all machining operations or materials. Their effectiveness can vary depending on factors such as cutting speed, feed rate, depth of cut, workpiece material, and tool geometry. It is important to evaluate the specific machining requirements and select the appropriate chip breaker design accordingly.
Usage Scenarios
Chip breakers are commonly used in various machining operations, such as milling, turning, and drilling. They find applications in a wide range of industries, including automotive, aerospace, manufacturing, and more. Some specific usage scenarios include:1. Milling Operations:
Chip breakers are extensively used in milling cutters, especially those used for roughing or heavy-duty machining. They help control the chip flow, prevent chip clogging, and improve the overall efficiency of the milling process.2. Turning Operations:
In turning operations, chip breakers are employed in turning inserts or lathe tools. They facilitate chip control and evacuation, minimizing the risk of chip entanglement, tool damage, and poor surface finish.3. Drilling Operations:
For drilling operations, chip breakers can be found in drill bits. They aid in chip removal and prevent chip accumulation within the hole, which can lead to drilling issues or tool breakage.In summary, chip breakers play a crucial role in chip control during machining operations. They offer advantages such as improved cutting efficiency, enhanced surface finish, increased tool life, and better chip evacuation. However, their design complexity and limited applicability in certain scenarios should be taken into consideration when selecting and implementing chip breakers in cutting tools.
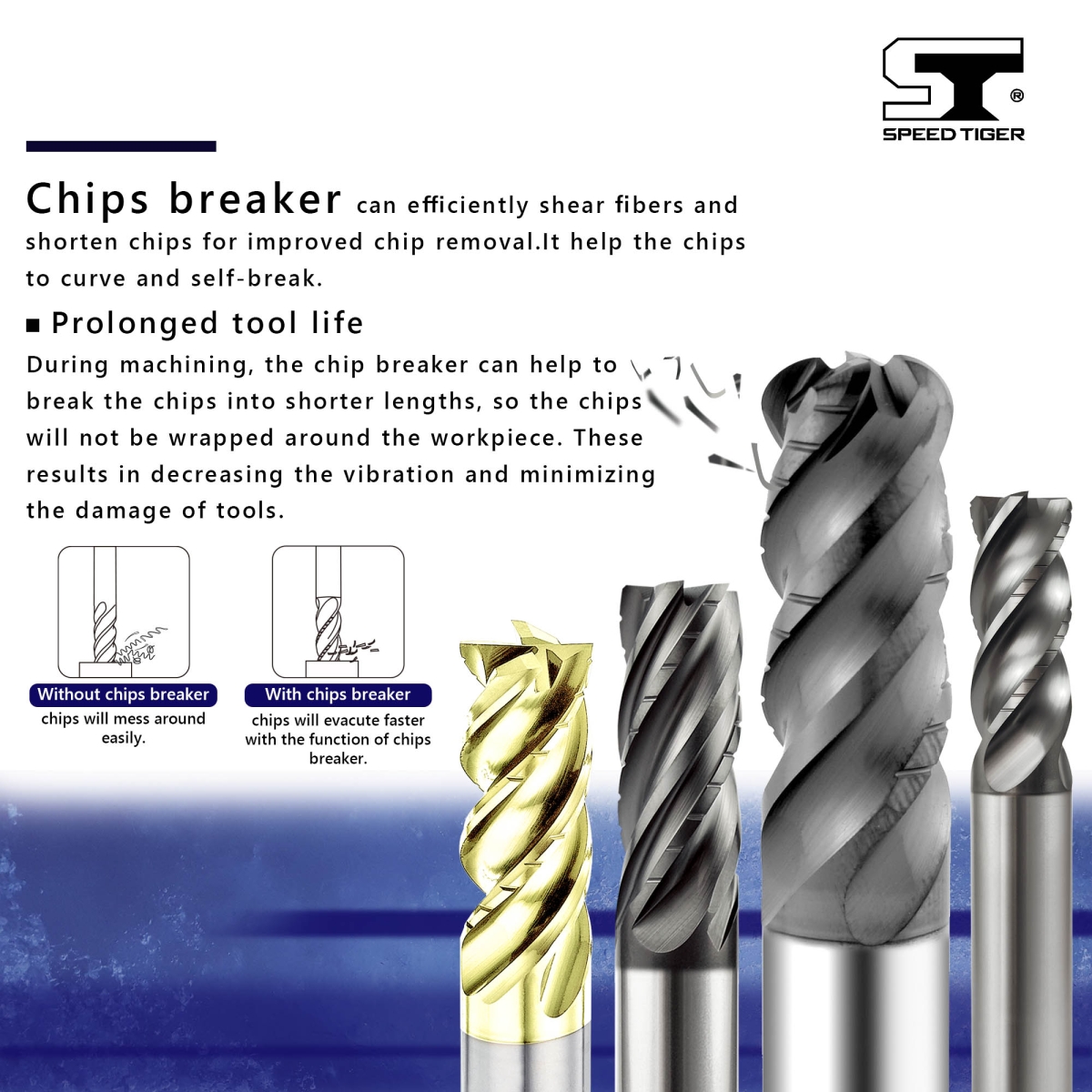
About Speed Tiger |
Speed Tiger is a professional manufacturer of Carbide Cutting Tools and offers OEM Services, having rich experience in producing carbide cutting tools and processing consultants for more than 24 years.
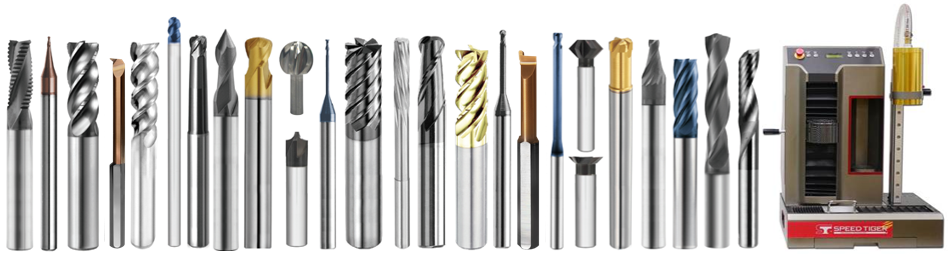
Established in 1998, Speed Tiger specialized in the production of precision carbide end mills, drills, turning tools, thread mills, and other tungsten carbide steel customized cutting tools. Speed Tiger crafts cutting tools at extreme nanometer precision +-2㎛ to the exact, enabling to achieve professional cutting quality.
Visit our shop to find out more, or check out our solution to continue learning.
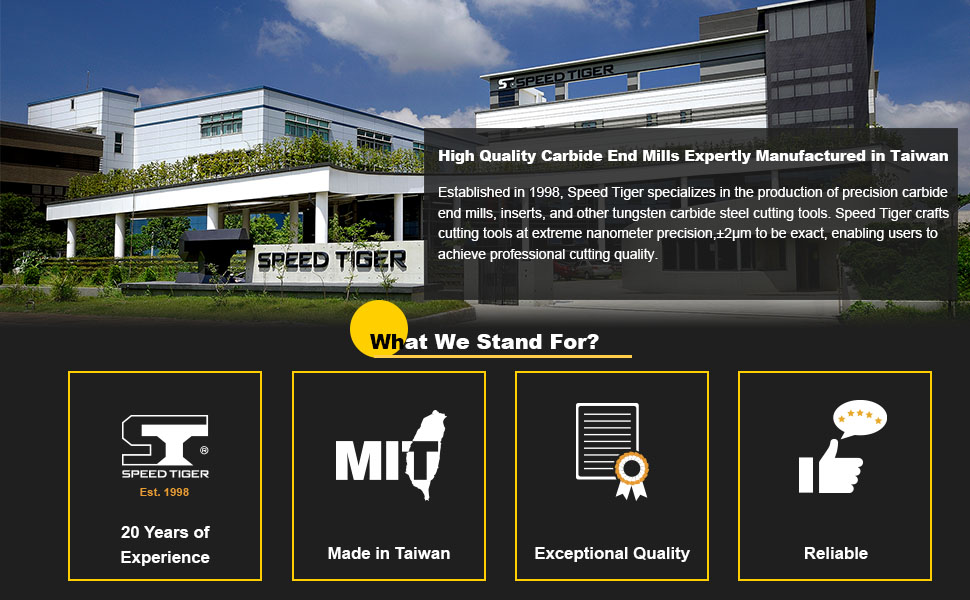
OTHER SOLUTIONS
-
What do End Mills coatings do Posted 2021-08-03
-
When Should I Use Flat Drills (Flat Bottom Tools) ? Posted 2021-04-09